Building & "Pimping" the burners
- Forge & Furnace Tumulus
- 13 jan 2019
- 7 minuten om te lezen
Bijgewerkt op: 16 jan 2019
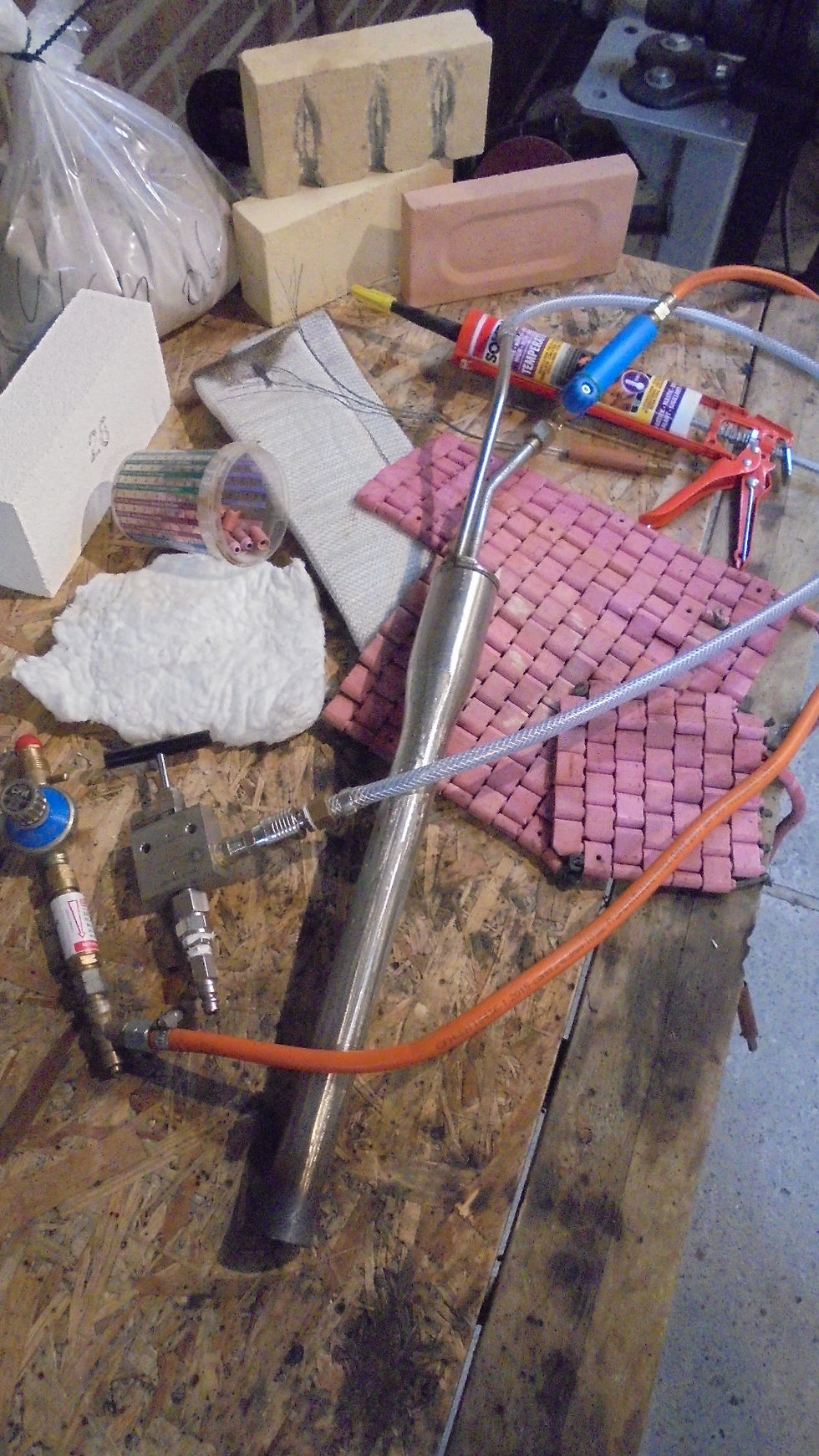
To fire my forges and furnaces I have constructed my own burners, using AISI 316 stainless steel or Inconel tube for the air inlets and mixing tubes. I got my inspiration from burners I’ve seen in oil crackers in the petrochemical industry.
I started by building an “atmospheric” (normally-aspirated) venturi burner, and later modified it to a “forced-air” (blown) burner design. This blog explains that evolutionary process.
The function of a venturi in a gas burner is fairly simple. Gas is supplied under pressure through a tiny orifice, and this jet of gas passes through a narrow spot in the burner called the throat, where it speeds up and creates an area of low pressure at the throat. The low-pressure area is lower than atmospheric pressure, so it draws atmospheric air in through an air inlet located ahead of the throat. The air then combines with the gas in the mixing tube to create a combustible gas/air mixture. This mixture is then ignited where it exits the mixing tube at its “mouth” or “nozzle.” It should only burn where it exits the tube and not within the tube itself. That explanation is an over-simplification, but it should give you a basic idea of the burner’s operation.
I have not included any scientific formulas dealing with BTUs required for operating forges or furnaces. Such formulas are of course available, and these formulas may take in to account several variables. For example, if the interior volume of a forge or furnace is too large relative to the BTU output of a burner, or if it lacks enough insulation, the forge or furnace may not get hot enough for its intended purpose. It’s also possible to over-fire a forge or furnace.
I used the above-mentioned materials to construct the burners because of their durability, heat resistance, and expansion/contraction characteristics. I believe they will hold up better than typical burners made from standard plumbing fittings and MIG-welding tips, as are often seen in online videos.
I used components of approved propane weed burners from the local hardware stores, such as the burner hoses, handles, valves, gas pipe, orifice, and mouth.
For the air inlet, I used a 4in (10cm) long X 2in (5cm) diameter tube, and for the mixing tube or “lance” I used a 12in (30cm) long by 1¼ in (32mm) diameter seamless tube. I flared the lance tube on both ends (using a conical hardy tool) to create a smooth transition to the air inlet at one end, and to make a nice burner mouth or “nozzle” at the other end. I constricted (necked down) one end of the air inlet tube to match the diameter of the flared inlet end of the lance tube and welded the pieces together.
I stitch-welded the cut-off weed burner tube to the end of the air inlet after drilling the air inlet holes to 3/8in diameter. Note: This is a called a “black-and-white” weld because it is between dissimilar metals (stainless and mild steel in this case), so I used 309 welding wire to make the weld, which has good heat resistance and is often used to weld 300-series stainless steel to carbon or low-alloy steels.
In one of the pictures you can see the sliding choke tube for adjusting the amount of incoming air, which is used to control the air/gas mixture to produce a good flame. Extra air in the mixture relative to the amount of gas (a leaner mixture) can make the flame an oxidizing flame. Less air relative to the amount of gas (a richer mixture) can create a reducing flame, which can also produce a lot of dangerous carbon monoxide (CO). The appearance of the flame cone provides a good indicator for getting the mixture correct. A CO detector can also provide a warning about an overly rich mixture and could also save your life if CO is building up in the air. Be sure to get one!
With this first burner design I was able to reach temperatures up to 2020°F (1100°C), which is a good working temperature for some purposes, but not hot enough to melt bronze or reach steel forge welding temperatures (such as needed for making Damascus steel).
To reach the needed temperature, I experimented with the position of the sliding choke and adjustments to the gas pressure. For feedback, I observed the appearance of the flame cone, listened for the response of a CO alarm (which could indicate a reducing flame and a big chance of CO poisoning), and watched the temperature readout from a thermocouple placed at the exhaust port of the forge or furnace.
After forging for a while with the above-described setup and considering my growing ambitions to melt and cast bronze, I decided it was time to ‘pimp’ the burners for even better efficiency. I had seen some forced-air or “blown” oil cracker burners (supplied with pressurized air from a blower instead of relying on a venturi to draw the air in), and I decided that it was time to make an upgrade.
Instead of a blower, my air source is a bank of air tanks, which are kept filled with an air compressor. The air from this “air bank” is supplied to the burner via a 3/8in tube that screws into a 3/8in nut welded over one of the air inlet holes of the burner. The air flow is regulated with a needle valve or a ball valve. With this simple setup and a slight increase of propane gas pressure from 15psi to 22psi (1bar to 1.5bar) I was able to achieve a temperature of 2500°F (1350°C).
All my equipment is now using my “Forced-Air Tumulus Burners,” and I’m currently building a couple of extra ones for possible sale.
Here are some specifications about the burners in addition to what has already been mentioned:
Orifice size is between 0.8 and 1.0mm (#67/#60)
Air pressure before the needle valve is at 3,5bar (50psi)
I have included the following important safety information. Please keep these points in mind, and be sure to read the disclaimer included in this post.
· Be sure to use an approved and functional carbon monoxide (CO) alarm in your shop/studio to warn you in time about CO building up in the air.
· Install a device to immediately shut off your gas supply in the event of a break in a hose or any other kind of failure that could cause the escape of a large volume of flammable/explosive gas or a sudden escape of gas.
· For all fittings and connections use only parts that are certified and allowed for use with propane gas, and use only joint tape or joint compound that is approved for use with propane gas.
· Install an approved propane “flashback arrestor” to avoid flame flashbacks from your burner into your hose or gas bottle.
· Make sure that there is enough distance/space between the burner and the attached gas and air hoses to prevent the hoses from getting too hot. After you shut down a burner, heat conduction and the chimney effect of the burner can make the burner and anything attached to it (or too near to it) dangerously hot. I suggest a distance between the burner and the hose attachments of at least 12in (30cm). You should check the temperature of the burner and attached components during operation AND after shutting down the burner and extend this distance if necessary. If a hose melts, it could cause a catastrophic escape of gas and a fire or explosion. Also remember that hoses that have braided steel exteriors may still have rubber or plastic tubes inside of them, which can melt if overheated and cause gas to escape through the porous steel braiding.
· After igniting the burner, make certain that the flame cone is generated only at the burner mouth (nozzle) and NOT anywhere else, such as anywhere inside the burner. A visual check and a temperature check are important. If a flame is burning inside the burner itself, it could indicate a problem with design or adjustments, or both.
· Position the burner mouth/nozzle so that it does not extend into the open interior of the forge or furnace. The end of the burner mouth/nozzle should not extend beyond the insulation/refractory material around the interior of the forge or furnace. Otherwise, it will soon be eroded by heat and/or oxidation.
· Use only clean and dry pressured air if you decide to use an air injection system like this one. Dust, moisture, and oil in the air supply can cause some serious problems, such as clogging or restricting the orifice, changing the air/gas mixture, creating dangerous emissions, altering the flame cone, and affecting the flame temperature.
· Be sure to wear personal protective equipment (PPE) that is appropriate for whatever activity you are involved with. This may include equipment for heat protection, breathing protection, eye protection, ear protection, fire retardant clothing, gloves, and more.
· Never operate the burners in confined spaces of any kind or in places without proper emergency escape routes. Adequate ventilation is critical for good air quality and your safety.
· Always have a properly-rated and checked fire extinguisher at hand.
Comments are welcome and appreciated. Feedback and suggestions from burner experts, the blacksmithing/casting community, and the general public are all welcome.
A popular and useful forum that deals with all aspects of blacksmithing, including gas forges and burners, is http://www.iforgeiron.com
With careful building and by following good safety rules, I think that my “Forced-Air Tumulus Burner” should serve you well.
Disclaimer – Please Read
All projects described here have been planned and executed according to best practices and common sense to the best of my knowledge. However, I am not a professional blacksmith, plumber, or LP gas technician. These devices are amateur experimental projects, and I do not warrant their safety, reliability, or effectiveness.
I have simply applied some ideas and technologies that I have encountered during my career, my own research, and trial-and-error experience.
Any use of the ideas, designs, materials, or construction techniques depicted or described here is entirely at your own risk, and you assume all liability for any damages or injuries that may result from that use.
Enjoy, and forge/cast beautiful things.
Excellent post, "Owens Heating & Cooling is a reputable company that specializes in AC repair and Furnace Installation Jefferson Iowa. With years of experience in the this industry, Owens Heating & Cooling has established itself as a reliable and trusted service provider in the field of heating, ventilation, and air conditioning. For more information visit our website.